Materials Used in PPR Pipe Fittings Production
In the realm of plumbing solutions, PPR (Polypropylene Random Copolymer) pipe fittings have become synonymous with durability and reliability. The choice of materials in the production of PPR pipe fittings plays a crucial role in determining their performance and longevity.
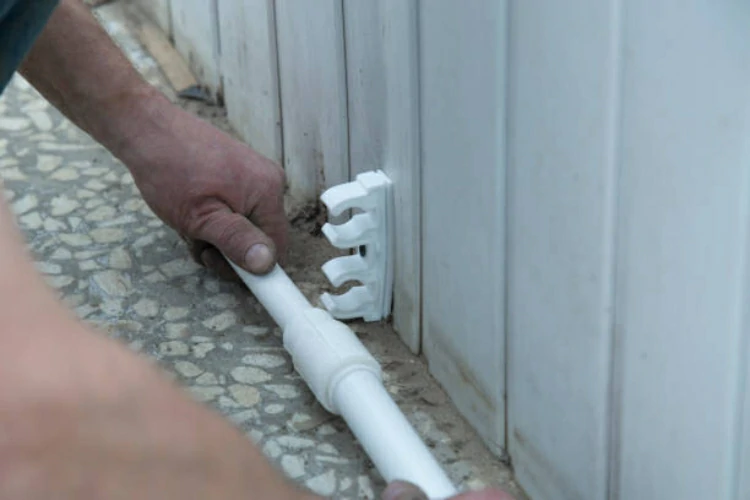
Polypropylene Random Copolymer (PPR)
At the core of PPR pipe fitting production is the use of Polypropylene Random Copolymer. This thermoplastic material is renowned for its exceptional properties, including high chemical resistance, thermal stability, and durability. The random copolymerization of propylene molecules during the manufacturing process results in a material that combines the advantages of homopolymer and block copolymer structures, providing a perfect balance of strength and flexibility.
Additives for Enhancement
In addition to the base PPR material, various additives are incorporated during the production process to enhance specific properties of the pipe fittings. These additives may include stabilizers, antioxidants, and UV inhibitors, contributing to the overall resilience and longevity of the PPR pipe fittings. The careful selection and precise incorporation of these additives ensure that the fittings meet stringent quality standards.
The Intricate Process of PPR Pipe Fitting Production
The production of PPR pipe fittings involves a series of well-defined steps, employing advanced techniques to achieve precision and consistency in the final product. Understanding the intricacies of this process sheds light on the quality and reliability of PPR pipe fittings.
Extrusion of PPR Material
The production journey begins with the extrusion of the PPR material. In this step, melt the Polypropylene Random Copolymer along with carefully selected additives and then extrude it through a die to shape the desired form of the pipe fittings. This extrusion process ensures uniformity in the composition and dimensions of the fittings.
Molding through Injection
Following extrusion, the molten PPR material is injected into molds through the process of injection molding. This step is critical in achieving the precise and intricate shapes required for various types of fittings. Injection molding allows for the mass production of fittings with consistent quality, meeting the demand for high-performance plumbing components.
Heat Fusion for Joint Integrity
One distinctive feature of PPR pipe fittings is their ability to form strong and leak-proof joints through heat fusion. During installation, heat the ends of PPR pipes and fittings and then press them together to create a seamless and robust connection. This heat fusion technique enhances the overall integrity of the plumbing system, minimizing the risk of leaks and ensuring long-term reliability.
Advantages of PPR Pipe Fittings Production Process
Understanding the materials and production process of PPR pipe fittings unveils the numerous advantages associated with these plumbing components.
Durability and Longevity
The use of high-quality Polypropylene Random Copolymer, coupled with precision manufacturing techniques, results in PPR pipe fittings that exhibit exceptional durability. These fittings withstand the test of time, providing a long-lasting solution for plumbing needs in various applications.
Chemical Resistance
The inherent chemical resistance of PPR material, further enhanced by additives, makes PPR pipe fittings suitable for a wide range of plumbing environments. They remain unaffected by corrosive substances, ensuring stability and reliability in diverse conditions.
Easy Installation and Maintenance
The extrusion and injection molding processes, combined with the heat fusion jointing method, contribute to the ease of installation and maintenance of PPR pipe fittings. The lightweight nature of the fittings and the simplicity of the jointing process make them a preferred choice for plumbing projects.
conclusion
In conclusion, the careful selection of materials and the meticulous production process define the exceptional quality of PPR pipe fittings. From the choice of Polypropylene Random Copolymer to the injection molding and heat fusion techniques, every step contributes to creating plumbing components that stand out in terms of durability, chemical resistance, and ease of installation. Understanding the intricacies of PPR pipe fitting production provides insights into the reliability and efficiency that these fittings bring to modern plumbing systems.
Contact:
IFAN is a manufacturer with 30 years of experience, specializing in plastic pipes, fitting, and valves in China. If you are interested in IFAN’s copper valves, PPR valves, pipe, and fitting, feel free to contact us. IFAN provides various standard pipes to meet your specific needs. Click the link below to explore IFAN’s diverse, cost-effective valve products, as well as related pipeline system products.
We will reply your email or fax within 24 hours.
You can call us at any time if there is any question on our production.
For more information,pls visit our webside https://www.ifanplus.com/
Pls Mailto: [email protected]